Abstract submitted to Pacific Basin Nuclear
Conference in Seoul, Korea, October 2000
The Windows-based PC simulator for Taipower's
Nuclear Emergency Exercises
Li-Chi C. Po, John M. Link and Frank Kenny
Micro-Simulation Technology
In conducting emergency exercises at its nuclear power plants,
Taiwan Power Company (TPC) has for years used large transient analysis
computer codes and training simulators to prepare the accident
scenarios. Neither is convenient and meets full requirements of the
task. Advancement in modern 32-bit microprocessors and Windows-based
graphic user interface (GUI) has completely revolutionized the
simulation technology. It becomes possible to automate the
preparation work and actual exercise on a desktop computer. TPC has
selected a PC-based simulation code PCTRAN [1,2] as the basis for its
plant specific emergency exercise systems for the plant Maanshan, the
twin Westinghouse 3-loop PWRs of 900 MWe each and the GE ABWR Lungmen
Project in construction.
The source code of PCTRAN was converted into Microsoft Visual Basic
6.0. Operation of the GUI follows strictly the specifications of
Microsoft Windows environment. Data input/output are in MS Office’s
Access database format. Reports and data can be transferred
conveniently through all Windows-based software products over the
entire exercise network.
Maanshan has sophisticated automatic control systems. The control
rod system and soluble boron control the core neutron
flux. Pressurizer heater and spray control the primary system
pressure. The Chemical and Volume Control System (CVCS) controls the
primary coolant inventory and water chemistry. On the secondary side,
steam output is controlled by the turbine control valve and steam dump
system. Steam generator water level is controlled by the feedwater
system. During the automatic control mode, they work in a
synchronized way so that transition to stabilized conditions will be
achieved smoothly. This has all been modeled in the PCTRAN
software. Operation is defaulted to the automatic mode. Operator can
take one of the control systems into manual operation by clicking the
corresponding manual button ("M") and a window will pop-up. By
entering a new set point, activating the manual action and closing the
window, that system will then run in the manual mode.
In the attached Windows displayed mimic of the Maanshan model, a
single loop is at the left side and the other two loops are combined
at the right side. The mimic also represents the controllable systems
as small panels with the important equipment shown as icons (i.e.,
pumps, valves, and heat exchangers). Design of the panels in the
mimic is limited to those critical to operations and emergency
functions. Other windows can be activated to display the radiological
release pathways, source terms, trend curves, P-T diagram (for PWR
subcooling margin), etc.
Important components such as the Power-Operated-Relief-Valves
(PORV) and safety valves of the pressurizer and the steam lines,
pressurizer spray valve and heaters, Main Steam Isolation Valves
(MSIVs), Turbine Bypass (Steam Dump) Valves, main and auxiliary
feedwater pumps and their isolation valves, Reactor Coolant Pumps,
etc. are displayed locally. Their control is by point-and-click on
the component using the mouse. A local window pops up for status
control to on, off, fail-at-mid-position, or even greater than 100%
(e.g. pump run-out). The status is indicated by color consistent with
the control room panel.
Control rod motion is animated. Pipe breaks are shown dynamically
by flashing sprays at the break location with the leakage flow
digitally displayed. Emergency systems include High Pressure Safety
Injection, Accumulators and Low Pressure Injection. Each one is
automatically activated when the plant condition demands so.
Operators can over-ride the automatic activation and manually control
equipment anytime during the simulation.
Preparation of the input files, selection of the initial
conditions, performing the transient analysis, graphic display of
plant status can all be conducted interactively and on-line. This
saves considerable time during preparation of an exercise and provides
a "live" tool during the actual exercise.
In order to demonstrate that the PCTRAN system truly represents
the Maanshan plant, verification benchmark analysis was conducted
for all FSAR Chapter 15 events. Reasonable agreement has been
achieved for each event. Success of the reactor physics and
thermal-hydraulics model formulates a solid foundation to further
expand into fission product transport.
The three major fission product barriers: cladding, reactor coolant
system and containment are modeled in the transport model. Transport
through various pathways such as containment leakage, steam generator
relief valves, turbine offgas and auxiliary building vents are
included. The radiological isotope iodine and noble gases at the four
release points formulate the source term. It will be used as input to
an offsite dose assessment model. The system uses actual
meteorological data and Maanshan neighborhood 3-D terrain to make dose
projection. Protection action guidelines such as food control,
localized shielding or evacuation are then decided according to the
dose projection.
An exercise scenario will be prepared by running the software in
fast-time to find a most-challenging script. During actual exercise
the Windows-based system will be re-run in real-time by the operations
personnel following directions of the planner. It will be tested in
the coming annual exercise at Maanshan.
References
- L. C. Po, "Analysis of the Rancho Seco Overcooling Event Using PCTRAN",
Nuclear Science & Engineering, 98, 154-161 (1988).
- L. C. Po "IAEA Activities in Advanced Reactor Simulation",
paper S1, the Fifth International Topical Meeting on Nuclear Thermal
Hydraulics, Operations and Safety (NUTHOS-5), April 14-18, 1997,
Beijing, China.
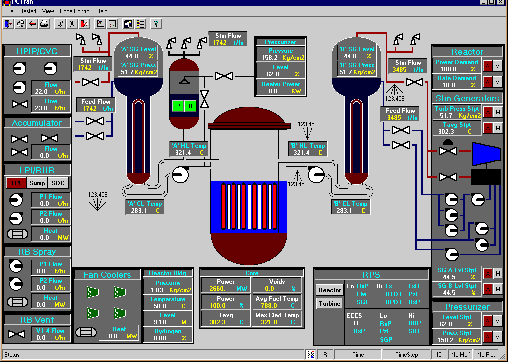
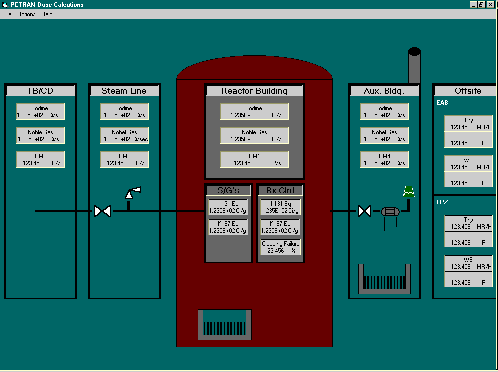
|
 |
|